- Posted on: 2020-02-19
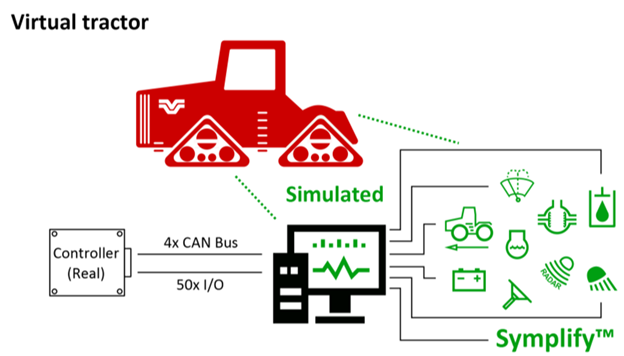
Our last few blog posts have focused on extending your embedded system ATS to add required capabilities for the decade ahead. In this blog we summarize a case study of Buhler Versatile, the largest Canadian manufacturer of agricultural tractors, that extended its ATS to accelerate testing.
Challenge: Increasing the reliability of testing and troubleshooting tractor production to shorten development cycles.
Solution: Developing a custom ATS using NI LabVIEW and CompactRIO with Synovus™ Symplify software to process and deterministically update more than 1,100 variables across multiple CAN buses to simulate multiple different tractor configurations.
Results: A 75% reduction in troubleshooting time, and a 30-fold increase in the frequency of testing through automation.
When Versatile approached our team to assist them with their challenge, we knew that our skills and the CompactRIO and LabVIEW platforms from National Instruments would allow our engineers to create the right solution for them. The initial requirements included over 600 variables (which grew to more than 1100) to process and update deterministically. These variables represented the status of digital and analog electrical signals, variables used in the models as well as signals received and transmitted on multiple CAN buses.
The ATS designed for Versatile includes a virtual copy of every component that the controller interacts with in a tractor (engine, wheels, etc.) Each of the models created in LabVIEW execute at fast loop rates in order to continuously update and read 500 CAN signals exchanged with the tractor’s controller. Custom logic, such as variable PWM signals, are implemented directly into the FPGA of the CompactRIO to mimic real components with micro-seconds (μs) accuracy. To support all of the configurations and options, some of the variables are used by the models to know which behavior should be replicated and which CAN messages should be transmitted.
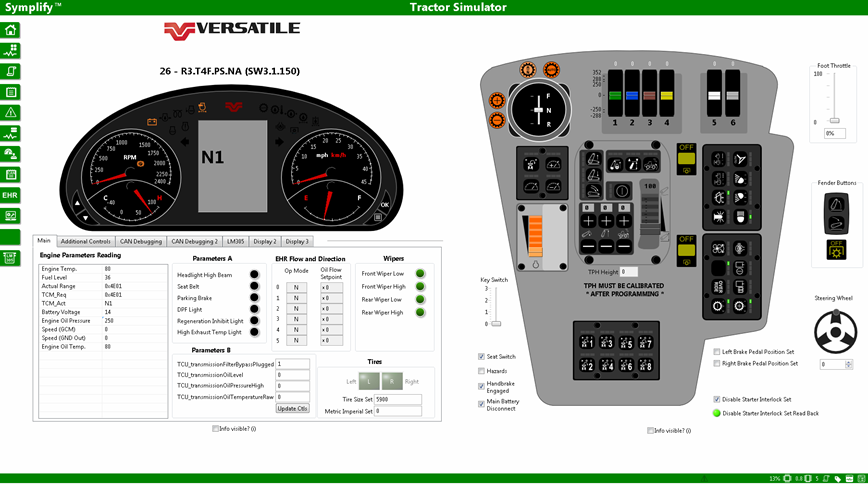
Benefits of this solution include:
- Parallel processing: The code for each model runs independently, executing in parallel threads to take advantage of multicore processors.
- Automating test procedures: Scripts automatically update variables (e.g. to simulate pressing a button) or read a variable to verify the controller’s behavior is correct (e.g. a specific CAN signal value). Such automated test procedures can be repeated every day without human interaction, saving thousands of man-hours and providing a reliable confirmation that issues have been resolved.
- Faster troubleshooting: You come up with questions and the ATS provides the answers. All variables coming from models, instruments and CAN bus are stored and can be displayed on multiple graph windows.
- New product development: The ATS offers Versatile new opportunities during the development of new products allowing them to reduce development time and deliver more reliable products.
- Increased reliability and significantly shortened development cycles: Versatile was able to increase its test coverage by 750% and detect bugs within hours rather than weeks. Another key benefit of the automated validation is that new tests can quickly be added to the existing suite of tests to increase coverage without increasing the workload of the validation process.
- Faster releases: Overall, Versatile expects the release process of new firmware to be 50% faster by taking advantage of the extended ATS features.
CTA: Read the full Versatile case study