- Posted on: 2022-04-04
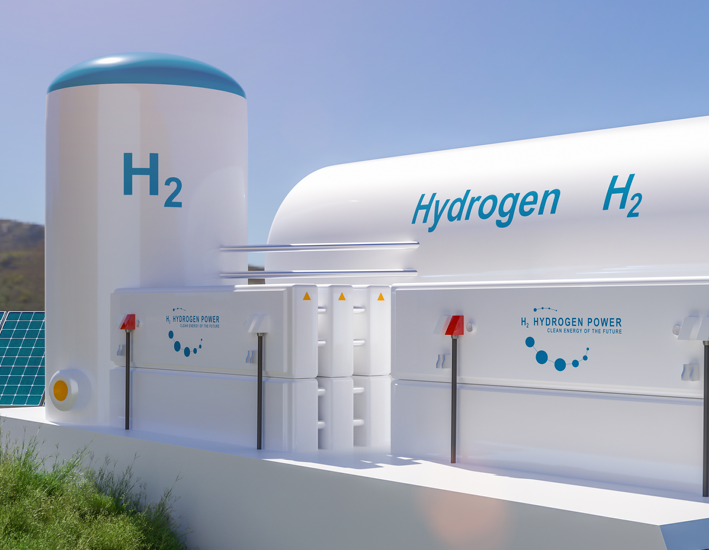
Are you looking to build your own Fuel Cell Automated Test Systems (FCATS)? Maybe it is because you require a greater flexibility in the controls or need to specify your own instruments. It’s also possibly that you wish to deliver your own solution to a growing market.
There are two main aspects to consider: the hardware for the station (electrical, mechanical and gases) and the software which offers most of the controls, protections and user interfaces. The objective of this post is to identify the challenges with the software that are not obvious from the start and explain why a flexible and reliable software platform will work best for your clients and greatly reduce your development efforts.
Controlling multiple instruments in real-time
FCATS is a great example of a system with multiple instruments from different vendors and various communication protocols. This is a clear sign that the control application needs to properly take advantage of multi-threading since some of the messages exchanged such as retrieving measurements can take up to a few seconds. In a simple, linear processing application, these delays can add up and make the system completely unresponsive. [un]Fortunately, most delays are neither large nor consistent and rather lead to various intermittent issues that range from annoying to dangerous.
Where should you start? NI LabVIEW is a natural choice for a development environment here since it was originally designed to control test and measurement systems and evolved into a highly versatile programming language. Its ability to communicate with various instruments through either SCPI, Modbus or CANopen and take advantage of multithreading by simply creating multiple “While loops”.
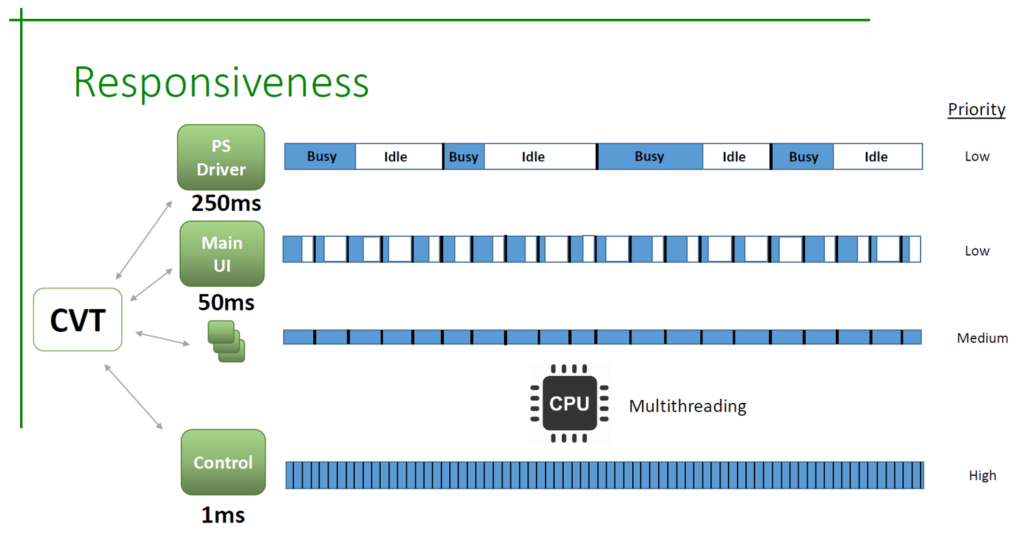
Handling and managing all the data
If LabVIEW is naturally a great choice to perform real time controls with multiple instruments, Symplify is the perfect extension when you also need to handle a large amount of data in real-time. A typical FCATS can easily require more than 1,000 variables before counting all the cell voltages and temperatures measurements. Those variables need to be used for many different functions:
- Closed loop control (PID)
- Data logging
- Supervisor
- User interface (control and graphs)
- Various other control functions
So what’s the best way to manage this information? Depending on some key decisions, it’s easy to end up creating new bottlenecks in the application and slowing down the processing in ways that are difficult to diagnose and resolve. Symplify was built from the ground to handle a large amount of data and we routinely that we can access 3,000+ tags (i.e. variables) from dozens of functions in parallel with no impact on the performance. Moreover, all the functions in the list above and many more are already developed and have been tested and validated.
Symplify also includes tools to quickly review and analyze your test results. You can quickly compare test runs from 3 months ago with the files continuously logged on disk or review the performance of your closed loop control at different gas flows. The tool also helps find relationships between test parameters and test results while automatically spotting differences in cell performance at similar conditions. If you are still using Excel to look at your data, you can give a try to our “TDMS Viewer” which also supports CSV/TXT files by downloading Symplify Now!.
A much higher starting point with Symplify
Symplify includes drivers that are already integrated within the platform. These cover NI DAQ instruments but also SCPI, Modbus RTU and more. Unlike the examples that lets you communicate with each instruments independently, these are already connected to Symplify’s Tag engine and can therefore immediately take advantage of key features for your FCATS station:
- graphing any of the data
- logging any of the data
- using any set points or readings from instruments in scripts to run test plans
- perform closed loop control through PID module on multiple instruments
This organization of the system’s variables and a constant monitoring on performance to locate discrepancy between the execution time and the desired control rate mean you can focus on your instruments and your test plans rather than troubleshooting complicated software!
Next step
Do you want to know more about controlling your MFC, heaters, loads, power supplies, pressure regulators and more in a short timeframe? Reach out to our engineers to discuss your application!